In 1872, Charles Goodyear fathered a machine that would be able to manufacture a highly resistant shoe that would be easily resoled. This marked such a revolution in the shoe market that this sewing method adopted his surname - GoodYear.
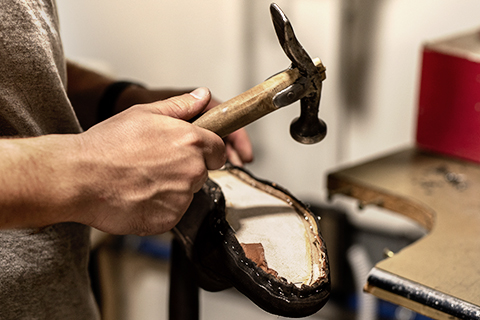
The Goodyear welt is the most laborious and durable method for the manufacturing of shoes (it is our favourite at Carmina). This can be done by hand or machine, however, both of these alternatives require highly specialized craftsmen. Following over 120 steps, it can take up to 4 whole days to manufacture a pair of shoes.
Nevertheless, a Goodyear shoe is well worth the wait due to the fact that one of the many advantages is being able to withstand time. The leather will allow the foot to breather and the cork insole will add that extra comfort as it will mould to your step. In addition, the whole process is characterized by the overlaping construction elements that will offer an uncomparable resistance.


What makes a Goodyear welted shoe so special and loved by the shoe experts? The secret is in the double welt.
The magic starts with the design of the patterns and the selection of the best leathers. Carmina Shoemaker is well aware that the use of premium materials will yeild a result of the highest quality. The previous cut leather will be sewn in the designed pattern in order to create the "Upper", the body of the shoe,( to which the welt is attatched. )
However, what really makes this manufacturing process so special is the sole.
The insole and welt will be sewn to the Upper. The welt is a strip of leather with an approximate 1,5cm width that will go around the whole edge of the Upper or only partly which will depend on it being a 360º or 270º welt. Once the welt has been placed, our craftsmen will proceed to cut off the excess leather.
The cork filling is next. This will allow the shoe to adapt your step after just a couple of days of use offering additional comfort and a personalized fitting. The Carmina craftsmen develop their own cork paste that is tucked into the space between the insole and the outsole. This is followed by inserting the metal shoe shank in the heel area in order to reinforce the shoe structure and offer a greater stability to the step.
Last, the leather piece to act as the shoe sole will be attached.
The shoe sole will be sewn to the welt and will be the base on which the heel will be set. At this stage, the sole has already been stitched twice. The first united the Upper with the welt and the second sewing connected the welt to the leather sole. This double attachment will allow a much easier resoling process as the welt acts as a muffler/shock-absorber between the insole and the outsole and can be completed with no special machinery.
This will allow the shoe's lifespan to extend to even decades considering a proper general caretaking procedure is followed. The additional stitches between the outsole and the Upper will offer a higher grade of water resistance and protection for the foot.
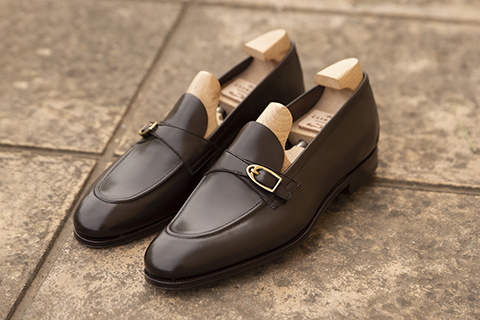
Carmina Shoemakers experienced craftsmen have even taken into consideration the weight of the components used in the construction of our shoes in order to create a lightweight Goodyear welted selection shoes which have been named "Soft welt" Collection.